Guest contributors Darioosh Naderi and Mark Marshall of Silicon Sensing look at how far the technology has come and why it’s poised to disrupt the market.
For years, manufacturers have focused on the consumer and industrial grade performance that MEMS inertial technology provides, with many in the industry assuming that’s as far as MEMS capabilities can take them. That perception is beginning to shift, though, with several companies proving their MEMS inertial sensors are capable of achieving tactical performance levels—and that’s changing the game.
When users switch to high-performance MEMS sensors, they’re often surprised with the results, Silicon Sensing’s Head of Business Development Darioosh Naderi said. The level of performance provided goes well beyond their expectations, with the solutions displacing fiber optics and other technologies, while demonstrating they can perform exceptionally well over a wide range of environments.
As strong as it is today, MEMS certainly hasn’t reached its limits. The technology has so much potential in terms of the capabilities and performance it can provide in the future, helping to solve many of the challenges the industry faces. Companies like Silicon Sensing are working to advance MEMS technology and unlock its full potential.
“There’s a state of flux right now, and companies are starting to go further with the technology,” Silicon Sensing Chief Engineer Mark Marshall said. “The accepted benefits of MEMS really are their lower size, weight and power consumption—as well as their potential for mass manufacturing, which keeps the cost lower than traditional inertial technology. Alongside these, two lesser-known benefits are their robustness and reliability—a consequence of the lack of moving parts in each unit. This means MEMS products will maintain performance in very harsh environments.”
Marshall continues: “There is no doubt there remains huge, untapped potential in MEMS-based technology, which has been limited to date by its ability to deliver market-disruptive performance.”
That disruption, however, is on the horizon as technological advances mean a number of inertial sensors are now demonstrating navigation grade performance.
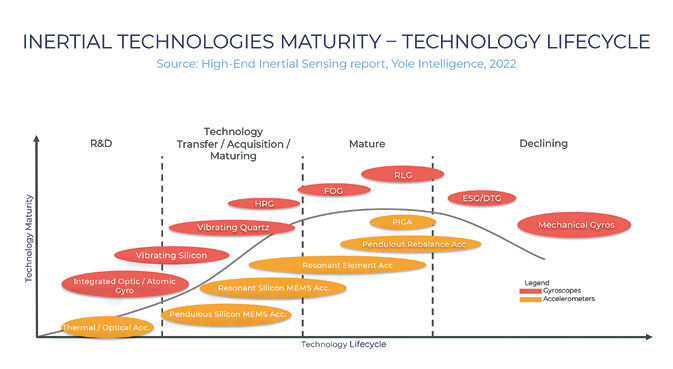
How MEMS Compares
There are various technologies that can be leveraged in inertial systems, all with pros and cons. “Mechanical gyros, for example, have been around for years and are a well understood, mature technology,” Marshall said. “But because they have moving parts, they need more maintenance, cost more, and aren’t as robust as MEMS alternatives.”
“Mechanical systems typically need to be recalibrated and must go through a certification period,” Naderi explained. “They may also require extensive maintenance, such as work to replace complex, well-balanced bearings.”
“Ring laser gyros (RLG) have advantages over mechanical systems,” Marshall continued, “with the biggest being their precision performance. RLG unit size can be an issue, but they are becoming smaller as manufacturing processes improve. However, they are not the most affordable solution. The cost of these devices is much higher than both mechanical systems and MEMS.”
“Fiber optic gyros (FOG), another option, have an inherently high bandwidth that addresses noise issues and delivers excellent performance. But, again, size can be an issue because it is necessary to wind a longer coil to achieve higher performance levels. They also have a higher price point.”
As the performance of MEMS inertial sensors continues to advance, this technology is now starting to offer the capability and performance levels needed by applications with much stricter stability and precision requirements. This is beginning to render them a viable and affordable inertial option, even for applications that call for tactical grade performance, and beyond.
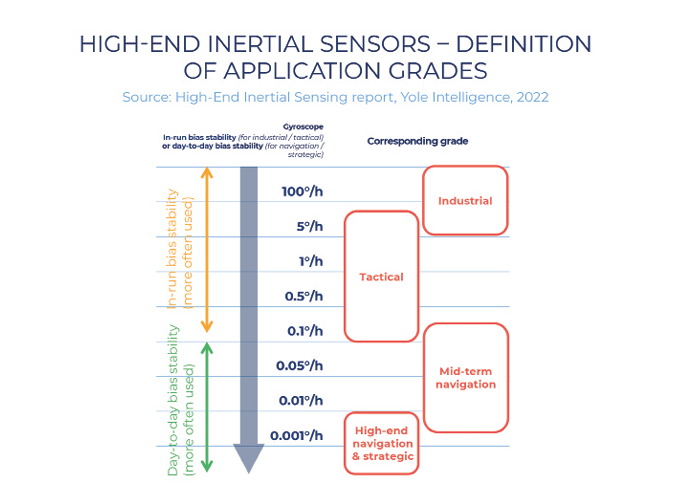
Getting to Navigation Grade
“Over the last 20 years, MEMS inertial sensors have continued to improve,” Marshall explained, “with improvements made in a variety of areas including bias, drift, noise, scale factors and angle random walk.” MEMS inertial sensors that have traditionally been used for industrial grade applications are finding their way into more tactical and navigation-grade applications that demand higher precision and lower drift rates.
“There are incremental improvements available today,” Marshall continued. “But we’re also focusing on that stepwise improvement, that order of magnitude improvement, that will see MEMS inertial sensors truly disrupt the market for higher-end technologies. Silicon Sensing is just one of many companies with a focus on working toward navigation grade inertial sensors at reduced cost, size weight and power (CSWaP) with encouraging levels of success.”
“For companies like Silicon Sensing, the real goal is to enable our partners to solve their guidance or navigation challenges, whilst recognizing the need to work with increased levels of signal disruption, an increased need for prolonged autonomy, and a requirement to operate in more extreme environments across land, air, sea and space.”
It basically comes down to solving two problems: Enabling users to gyrocompass in an often intense, dynamic environment, and providing aided navigation in a frequently GNSS denied environment.
“Today, you can take a Silicon Sensing MEMS sensor and rotate it around a step motor to find true north,” Naderi explained. “This is ideal for users, such as the downhole drilling market, who need to know where true north is quickly and unaided.”
“Right now, companies are paying tens of thousands of dollars for complex and costly systems that allow them to gyrocompass when in reality they might not need all the performance their chosen solution provides,” he said. “Similarly, they may not be able to use a magnetometer because, while the performance may be sufficient, it may be too susceptible to local magnetic fields. The ability to provide a device that is capable of true north seeking without external aiding, doesn’t suffer from local interference, and has the size and price of a MEMS unit will significantly disrupt the market.”
“To solve the gyro-compassing problem, solutions need to offer sub-one degree an hour for residual bias,” Naderi explained. “But for navigation-grade performance, you have to get much lower, again with different markets and applications having different requirements in terms of performance.”
“The main goal is to get bias and associated parameters as low as possible. This will give us that order of magnitude ‘stepwise’ improvement Mark talks about needing to achieve,” Naderi explained. “Improving noise and scale factor are also priorities.”
“And that’s where you say: What problems are you trying to solve and what are your key parameters. Most will say they are scale factor, bias and angle random walk,” Marshall said. “If you look at our gyro technology as standalone sensors with their own electronics, we are closing the gap to navigation grade in many parameters today. Some of our customers are virtually there without any aiding sources and without any mechanical rotation or gyrocompass. They are about to cross that threshold. But that’s just the gyros. There are also accelerometers to consider.”
Extremes of temperature is another key consideration.
“It’s not just sitting on the bridge of a vessel at 25 degrees Celsius forever,” Marshall said. “Getting the sensors to work in any environment, from minus 55 degrees all the way up to plus 85 degrees, is a real challenge. We have customers operating at all temperature brackets—and in even more extreme situations.”
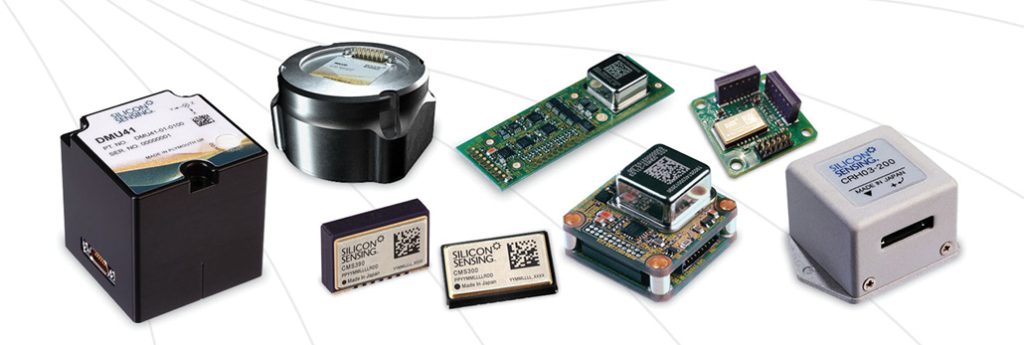
A Look at the Market
Today, the main customers relying on tactical MEMS for an IMU are the surveying and mapping markets,
marine gyro-compassing customers, and defense applications for guided munitions, Naderi explained. “One of the biggest markets primed for disruption is avionics. The performance parameters that must be met are clear, and while this won’t be easy, it is within reach for MEMS manufacturers.”
The aerospace market is an obvious candidate for MEMS, Naderi believes, along with broader defense applications such as tactical wheeled vehicles and any theater of conflict where GNSS jamming and spoofing are concerns. In fact, MEMS would have application almost anywhere a ring laser gyro is currently in use.
And because MEMS technology is a fraction of the price and size of other options, “it opens doors to applications tomorrow that we don’t even know exist today,” Naderi believes.
“We could be creating new applications. Just one area with huge potential would be in the growing unmanned markets,” Naderi said. “Longer endurance and beyond visual line of sight is becoming more feasible. And when you have a navigation system that doesn’t rely on a constant external input, it presents so many new opportunities. It disrupts by definition.”
Advancing the Technology
Silicon Sensing already has a patented high-performance gyro that has gone through multiple design iterations. Just one area the company is focused on today is material use, Marshall explained. “A key avenue we’re looking at is new novel materials in the MEMS structure itself. That’s something we believe there’s quite a bit of mileage in. There’s really some exciting work going on.”
This includes looking at the detailed construction of the gyro and how the layers are made up, exploring re-positioning the MEMS within another structure with the ASICs to control them, and working on complex discreet electronics to drive the gyros optimally such as improving how information outputs are delivered. The company is also making advances in the way sensors are calibrated.
“So, we are looking at a whole system on every front and we’re seeing many innovations we can introduce,” Marshall said.
Critically, the company is also exploring improvements for more efficient volume production.
Silicon Sensing has three different modes of operation for its gyros, Naderi explained. Some are driven with magnets, some are capacitive and others use a thin film PZT material.
“If we look at the inductive gyro, we can improve the magnetic circuitry in it and gain benefits in the scale factor almost immediately,” Naderi said. “If we look at the design of the gyro, which is on a base, and if we change the base without changing the fundamental design, that gives us benefits in terms of bias. So, we can take the exact existing design, existing manufacturing process, make a minor tweak, and that can give, in some cases, a three-fold improvement. And we can do that today.”
“MEMS feature layers of material, including silicon, metal and glass,” Naderi said. “The thermal characteristics of these different layers is a key area of consideration. Manufacturers can look at different techniques to try to improve on existing designs without going back to the drawing board.”
“You look at the improvements we can make to an existing drive type, with the magnet and with the structure it’s on, then you look at the material mismatching, so already you’ve got some ground,” Naderi said. “Then you look at the capacitive type gyros that are three millimeters or four millimeters, we can make them larger, and possibly apply some very clever real-time balancing techniques. And we can get a sense of a performance improvement that could be four times better than we have today. Versions of these sensors have been built and tested. Our focus now is on bringing that product to market with a set of electronics that will get the best out of the sensor, whilst maintaining the attractive size and cost of a typical silicon MEMS inertial product.”
Steering the Development
Silicon Sensing has its own MEMS foundry, enabling the company to produce parts at a much lower cost and at higher volumes. It also allows them to be far more involved in the design and manufacturing than those who outsource production.
“We have the flexibility to be able to tweak the designs and we work very closely with the foundry processing, calibration and engineering teams. We have ultimate control,” Marshall explained, “so we can do all the finite element modeling and we can steer the development.”
The foundry’s sole purpose is to turn out MEMS inertial sensors, Naderi explained, so the team has acquired a wealth of knowledge about the products that a third-party foundry just wouldn’t have.
“It could take years to get a prototype that ticks all the boxes out of a third-party foundry,” Naderi said. “Our foundry has a very quick turnaround, speeding up product development and time to market. And it is a powerful asset, having decades of knowledge and foundry expertise.”
Looking Ahead
In the next three to five years, Naderi expects to see more companies pushing toward navigation grade MEMS offerings, with those small, iterative steps making revolution possible. The disruption these sensors will cause is closer to five years out. It comes down to putting everything together in a package that delivers what’s required and costs significantly less than alternative technologies. Accelerometers are also advancing. Silicon Sensing is working on offerings that have the required performance, with some promising initial results. However, formal qualification programs take time, as do the vital updates to production lines that will allow reliable production of these much higher performing sensors.
“In some respects, the design of a navigation grade MEMS gyro exists today. Bringing it all together in terms of the drive electronics and reliable, full-scale production is our main challenge,” Naderi concluded.
Authors
Dr. Mark Marshall was appointed Chief Engineer of Silicon Sensing Systems in February 2023 having joined Silicon Sensing in 2017 as the lead engineer on numerous inertial programs. Previously, Dr. Marshall worked as a senior research engineer in the field of laparoscopic electro-surgical instruments, with many patents and refereed papers. He has a first class honors degree in Computer Aided Engineering, an MSc in Advanced Manufacturing Systems and a PhD from the University of Cambridge.
Darioosh Naderi is the sales, marketing and business development lead for Silicon Sensing Systems Ltd (SSS). SSS is a leading provider of silicon micro electro-mechanical systems (MEMS)-based inertial sensors and systems, including gyros, inertial measurement units (IMU) and accelerometers. Mr. Naderi has worked in business development and product strategy within Silicon Sensing, and within one of its parent companies, for some five years.