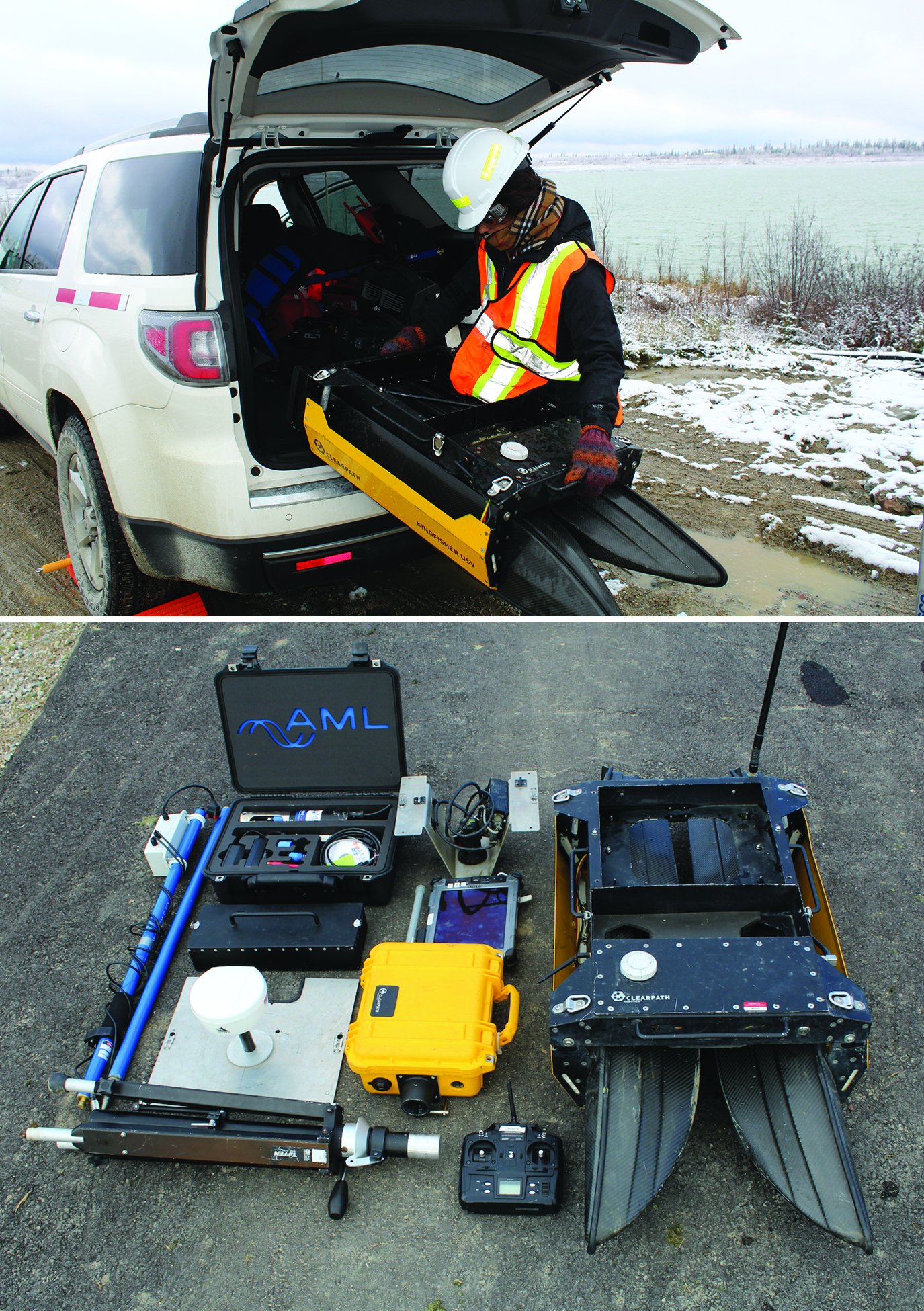
“Our products are robotic research platforms,” says Clearpath’s Meghan Hennessey. “These can be configured and programmed so that our customers can explore their particular areas of interest without all the cost and troubleshooting involved in actually building robots themselves.”
Hennessey says Clearpath platforms — which include the all-terrain Husky, the larger, tractor-like Grizzly and the waterborne Kingfisher — can be thought of as project kits.
“Our products are robotic research platforms,” says Clearpath’s Meghan Hennessey. “These can be configured and programmed so that our customers can explore their particular areas of interest without all the cost and troubleshooting involved in actually building robots themselves.”
Hennessey says Clearpath platforms — which include the all-terrain Husky, the larger, tractor-like Grizzly and the waterborne Kingfisher — can be thought of as project kits.
“We build the hardware and then we integrate whatever sensors and other components our customers may require,” she says. “They can then program these platforms for their own specific applications or research projects.”
With the latest GNSS technologies built in, Clearpath robotic platforms are capable of remotely piloted and autonomous navigation — vehicles with the intelligence to travel safely outdoors without getting lost and without the need for constant control by a human operator — making them highly flexible tools for many applications and environments.
“Our customers are also interested in looking at how robots interact with people,” Hennessey says, “and how they can serve to assist workers in hazardous or difficult jobs, from mines to hospitals.”
One of Clearpath’s clients is the Massachusetts Institute of Technology, where students developing software for larger boats in open water use the Kingfisher to test their programs, making sure that their software and algorithms work before moving on to larger vehicles.
Clearpath is also a longstanding partner of the Open Source Robotics Foundation (OSRF), working within the community to provide open-source software based on the Robotics Operating System (ROS) platform. The software is posted publicly and then continuously maintained and improved by other members of the community, which allows researchers to build upon the experience of the entire academic community and push the limits of robotics research farther and faster.
Professional Applications
But the Clearpath experience is not all about academic research.
In 2014, the company split out its bathymetry unit into a separate subsidiary called Echostream. While Clearpath continues to deliver the Kingfisher as well as ground-based vehicles to research-oriented clients, such as MIT, the University of Ontario, and the University of Oslo, Echostream offers the Kingfisher as part of a remote sensing system to help water resource professionals collect and analyze bathymetry data on inland waterways.
Blyth Gill, Echostream’s commercialization manager and main technical lead, interfaces regularly with the engineers at Clearpath.
“A lot of the other platforms out there provide a part of the solution,” he says. “That is, you get a platform that has a sonar and a GPS and you’re going to get basic data out of it, and then you’ll have to process the data with survey software and have an expert on hand to deal with the kind of unique cases that come up.”
Every underwater survey is different, Gill says, and his group benefits greatly from the intimate knowledge it has of Kingfisher hardware, its software, and of the entire data collection process, enabling them to whiz through a lot of the data cleaning and data processing for their own purposes and that of customers.
“We’re getting tens of thousands of bathymetric data points, compared to traditionally hundreds of points for a particular survey,” he says “So, there’s an intentional step of reducing the number of points, selecting only the best data.”
Design Challenges
Weighing just over 60 pounds (28 kilograms) with its 14.4-volt NiMH battery, and measuring 1.35 x 0.98 x 0.32 meters (51.2×38.6×13 inches) when deployed, the sturdy Kingfisher is small enough to fit into just about any car, SUV, helicopter, or plane. For experienced users, it takes about five minutes to set up on site.
Gill says Clearpath engineers faced a number of operational hurtles in designing and building the waterborne robotic system.
Commercial vessels of this size are uncommon; most are larger by a significant degree. So, the engineers were unable to rely on existing industry best practices.
“We had to undertake a great deal of theoretical and experimental modeling of both the hull and thruster system,” says Gill. “In addition, there are a number of other aspects that don’t scale down in a favorable way. For example, the vessel control system takes up a proportionally larger amount of the craft’s payload capacity and power budget.”
The Kingfisher’s intended operational environment and the absence of a crew onboard also posed challenges. Basically, the system had to be visible at range, it had to be hand-launchable from shallow water and, most importantly, it had to be able to resist environmental fouling in a relatively power-efficient manner.
Driving remotely using the Kingfisher’s 2.4-gigahertz wireless connection means that size and visibility are also issues. Humans have a very hard time perceiving distances towards the horizon, he points out. “Once [the Kingfisher] is 400 meters across a lake, it becomes difficult to make out the vessel’s position and attitude. Trying to identify how close the Kingfisher is to the other shoreline can also be a real problem.”
But even when visibility is not a problem, operation of an unmanned vessel is not intuitive as the pilot is not on the craft and does not share the same perspective as the boat’s position and aspect. “Most people who have driven the Kingfisher have, at one time or another, commanded it to turn to port when they meant starboard,” says Gill.
Finally, variable water and wind conditions can affect speed, rendering control of the vessel difficult. A throttle value does not relate directly to a certain speed, making it a challenge to set the robot to a desired consistent speed.
The Right “Stuff”
Part of Echostream’s success has involved choosing the right components, including an advanced dual-frequency GNSS receiver able to receive and process both GPS and GLONASS signals as well as those from an L-band satellite-based augmentation system (SBAS). Gill says Echostream had a very specific technical requirement — OEM equipment that could operate employing multiple techniques and resources, such as virtual reference stations (VRS), real-time kinematic (RTK) mode, and satellite corrections.
The VRS technique generates in real time a virtual reference station at or near the initial rover position. This is done by geometrically translating the pseudorange and carrier phase data from the closest reference station to the virtual location and then adding the interpolated errors from the network error models.
“We also provide a ‘base-station’ for our own system that provides RTK positioning, separate from the GPS unit,” Gill says.
The Kingfisher’s OEM GNSS module is very easy to program.
“The unit we selected is highly customizable,” he says. “It doesn’t have a lot of the bells and whistles that survey-grade GPS units tend to have.”
Because the unit is mounted on a surveying platform — the Kingfisher — it doesn’t need things like battery packs or Bluetooth. The Kingfisher is linked to a powerful computer and has a very large battery.
“We need certain NMEA messages output over a serial port and it’s incredibly easy to configure our GPS unit to output these data streams,” he says. “We basically can set it and forget about it.”
Gill says that Clearpath has had issues in the past with so-called “survey-grade GNSS” where, because they’re pre-configured to be used in a dynamic way, “it’s very easy to accidentally change settings, and then you get problems. With our unit, there are no issues with its being mistakenly reset. So, it’s nice to be able to configure it once and know that, when you send it RTK corrections, it’s going to go into RTK mode and then relay the message types that you need over the serial port as designed.”
The Kingfisher has also has an OEM inertial measurement unit (IMU) on board, linked to the GNSS receiver. It uses rate gyros, accelerometers, magnetic sensors, and an onboard 32-bit ARM Cortex processor to compute sensor orientation 500 times per second. The inertial unit is able to interface with the GNSS module to provide position, altitude, speed, and course outputs, using industry-standard NMEA sentences.
“The IMU is used for a sensor fusion step to trigonometrically correct sounding depths and positions for pitch and roll,” Gill explains. This is a key capability in many bathymetric applications, where the survey vessel is in constant and often irregular motion due to wave and tidal action.
Impossible without GNSS
Localization, which supports autonomous guidance and navigation in a body of water, can be a very difficult task for many reasons. Water bodies are ill-defined in the sense that their perimeter and the presence of obstacles can change within hours or a day depending on water level. Obstructions are often below the water level, presenting a challenge for sensing equipment to identify them.
Even on small lakes and ponds, the closest geometrically distinct features might be on the shore, which are often ambiguous, i.e., vegetation along the riparian zone is difficult for a sensing system to differentiate. With this in view, Gill says the Kingfisher system would not have been possible without the GNSS module, with aiding from an onboard inertial measurement unit (IMU) in a waterproof enclosure
Highly accurate GNSS with a low update interval provides a simple way to determine an unmanned vessel’s velocity. Reporting the speed is as easy as sampling the magnitude of the difference between positions over time. This, along with known vessel position relative to pre-existing imagery, topography, or water body geometries, gives the user immediate feedback to vehicle controls.
“GPS can describe where the vessel is with relation to a common datum,” Gill says. “Aerial and satellite imagery and other geospatial data can be loaded into mapping software along with the real-time position of the vessel to provide the driver with a clear understanding of the robot’s situation.”
As he explains it, traditional surveying before GNSS involved tying into a control point and using a theodolite or, more recently, an electronic total station or a robotic total station.
“You’d basically just had errors stacking up,” he says. “You’d have your one position and then you’d find a position relative to that and do some trigonometry. And then you’d put lines across your water body and then get in the water and try and do every meter across a line. You’ve got your ‘x’ and your ‘y’ or your lat[itude] and your long[itude] and then you measure a depth. And that’s all pretty complicated, and there’s a lot of error that can [accumulate]; it’s a very manual task.”
Because Kingfisher has GNSS onboard, every single measurement being made by the sonar can be related directly to a GNSS measurement.
“This is great in two ways,” Gill says. “First, we’ve got very precise latitude and longitude, to about one to two centimeters accuracy; so, that’s much better than trying to do this relative to a local control point, which may be very far away. You may not have one available; you may have to just tie into a head wall or something and then all you have is relative data. Meanwhile, [with GNSS] we can tie our data into the WGS 84 ellipsoid.”
Another benefit, Gill says, is GNSS’s high vertical accuracy.
“Because we have very good vertical accuracy, what we are essentially doing is using sonar to measure the distance from the GPS to what’s being surveyed at the bottom of the water,” he explains. As a result, the Kingfisher operator doesn’t need to worry about the water level or sea level.
“Traditionally you would have to say, ‘Here are all the depths relative to the sea level,’ then you would have to do mean sea level calculations, and more error stacks up there,” says Gill. “So, it’s fantastic [to be] able to completely ignore water level when doing these measurements.”
The extreme precision now available with GPS, and especially the vertical accuracy, allows today’s surveyors to “subvert many generations of how we used to do bathymetric and hydrographic surveying.”
Additional Resource
Kislig, L., “What is a virtual reference station and how does it work?” GNSS Solutions, Inside GNSS, July/August 2011