A Culture of Innovation
Michael Ritter isn’t afraid to take risks in the name of innovation. And flying a fighter jet with your sensors, employees and a reporter onboard certainly qualifies as risky.
There’s a culture of innovation at Hexagon| NovAtel, so when the marketing department formulated the idea for the extreme flights, there wasn’t any hesitation. It took time and resources to make these tests happen, and so much could have gone wrong. But that risk of failure was part of the draw.
“Trying things without knowing what the outcome is,” said Ritter, who’s president of Hexagon’s Autonomy & Positioning division, “that’s a teachable moment for engineers. If you know what the outcome is, that’s not really innovating.”
The data collected will not only be used to develop better products for customers, it will help employees truly understand their needs.
“Everybody likes to innovate,” Ritter said. “But you can innovate better if you actually know the real customer experience.”
The two employees who rode in the L-39’s jump seat now have a better understanding of customer requirements and what their equipment goes through. They know what 4-g and 5-g thresholds really mean because they’ve now experienced them.
It’s no longer something they’ve only read about in a textbook or simulated in a lab. And there’s real value in that.
Then there’s the verification piece. It’s critical to test sensors in high dynamic environments—and what’s more high dynamic than a high-performance fighter jet?
“It validates our simulation models,” Ritter said, “which is really important because it means we can test a lot of different operational modalities on new products and in simulation.”
This isn’t the first time Hexagon| NovAtel has gone to extremes for product development, and it won’t be the last. These types of experiments create an intersection of innovation and motivation that drives team members to excel, and to talk about the unique opportunities they have at work to family and friends.
“It’s part of recruitment,” Ritter said. “People reading this article will say ‘wow, they do that?’”
Yes, they do that.
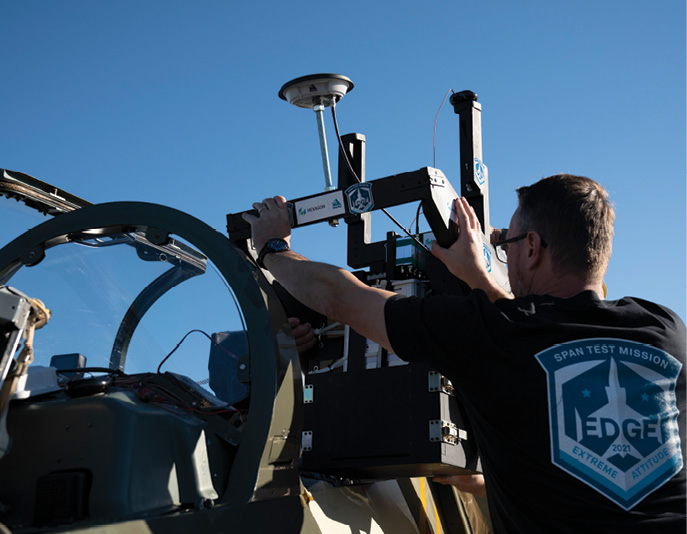
Testing the Limits: Plotting a Course into the Wild Blue Yonder
PART 1: Planning Phase
To determine the limits their equipment could perform to, Hexagon | NovAtel engineers developed a plan to put the company’s sensors to the ultimate test: fly them aboard a Aero L-39 Albatros.
When Hexagon | NovAtel product design engineers set out to architect the kit that would endure extremes of high-dynamic operations on board the Aero L-39 Albatros, they began with a high-end concept.
“We know we’re always looking for extreme tests and crazy corner cases, for our SPAN products, particularly,” explained Gordon Heidinger, segment manager, automotive and safety-critical systems. He referred to the company’s well-known integration of GNSS and inertial technologies, a deep coupling recognized for continuous 3D position, velocity and attitude.
“And our other products, too,” he added. “Any of our positioning solutions for that matter. These extreme tests are always exciting and fun to do.”
“The best of our best [SPAN systems] is probably going to perform really well. I don’t expect any issues with the top-end stuff. But how good is the other stuff? And is it good enough for these dynamic conditions? If we can survive a fighter jet, I can sure as heck put it on a car or some UAV that’s delivering pizzas.
“We’re looking at high Gs, we’re looking at inverted flight,” Heidinger said in Calgary, when the testing, which took place last December in Florida, was still in its planning phase. “This is really going to highlight the sensor fusion elements of our SPAN solutions.”
The architecture of the equipment under test brought together high-level, mid-level and low-level inertial measurement unit (IMU) solutions side-by-side in one bolted-together piece of equipment. An important control aspect of the tests was data capturing a radio frequency (RF) recording of everything going on.
“That’s for development of future products that I can’t talk about yet,” Heidinger said.
Three IMUs, High-Dynamics Testing
Chosen for the side-by-side testing were a well-known navigation grade IMU at the high end of the range, another widely used IMU in the mid range of accuracy, performance and cost, and then on the lower end, a popular MEMS IMU.
The tests weren’t developed to compare performance among the three IMUs, even though they performed in parallel, side-by-side. It was about taking the equipment to the limit, taking it past its limits and then being able to look back and say, “that’s where it stopped performing at the level I need it to perform.”
Ultimately, the goal was to answer the customer question: What product is good enough for my application?
As drones and other technologies become more dynamic, it’s important to know how good good actually is, and how far sensors can be pushed for applications with high dynamics.
“It also introduces more people on our teams to some of the experiences closer to what a customer would experience,” added Stephen Dwyer, systems engineer, Hexagon | NovAtel, “as compared to living in the relative luxury of a lab type test setup. Those situations where you have every instrument at your disposal, all the bandwidth in the world to collect data that you need, that’s a luxury that a customer doesn’t necessarily get, or need, frankly. And so being able to empathize with a customer when they’re trying to do a complex setup, I think that’s pretty important for driving easy-to-use products in the future.”
One of the challenges NovAtel faces is being able to test outside of typical land-vehicle dynamics situations. “We don’t get access to those high dynamics that you see in a fighter jet,” Heidinger said. “So, the high speeds in hundreds of miles per hour, that may not coincide with what our customers are using them for in small UAVs, this provides us with at least a similar dynamics environment.”
While NovAtel has a lot of equipment riding aboard many aerial applications like this, the company’s customers, many from the defense branch, cannot share the classified performance data. “So here’s an opportunity we made for ourselves to be able to access and use that data freely, because we paid for it,” Heidinger added.
“Another thing about being able to control the data collection,” Dwyer said, “as opposed to getting data from customers, is we get to more tightly control some of our data that we’re collecting, the rate of that data, and some additional debug data that we might not necessarily get from a customer application. And it’s going to be very interesting to see some of that higher fidelity information that we get back from the test, compared to what we normally see.”
The L-39 can customarily pull 4.5 to five Gs of gravitational force during its most demanding maneuvers. That kind of stress reveals what measuring instruments are capable of. NovAtel has done previous comprehensive testing that has been necessarily restricted to the lower G area. Getting double or triple that G loading will definitely be informative.
“If what we predict is going to be met in terms of performance at these key levels, then it definitely gives us much more confidence when we’re moving into even those higher performance specifications or higher dynamic range conditions,” Dwyer said.
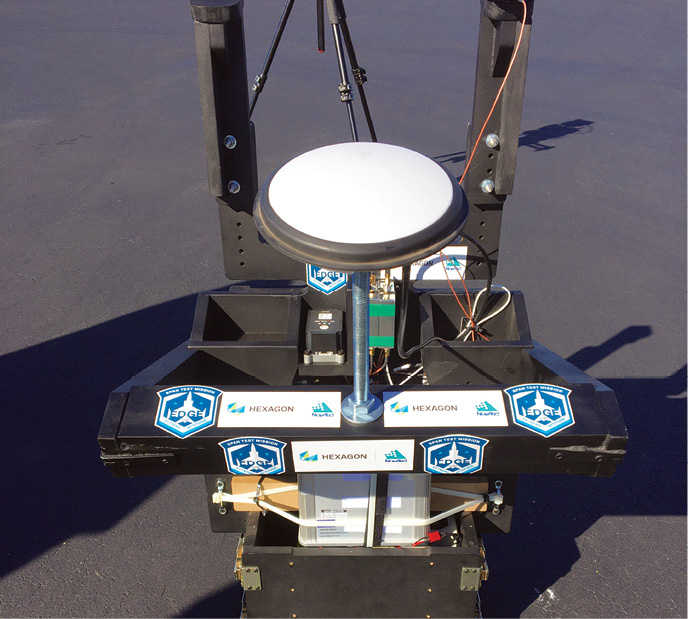
Test System Design
The fighter jet was booked for three 60-minute flights over two days of testing. All three IMUs simultaneously experienced the same flight, three times over. One of the complicating factors was the limited space inside the cabin of the and not being able to modify the aircraft by bolting equipment to its chassis or fuselage. The experiment designers had to fashion a human-resembling apparatus that could be securely strapped into a passenger seat. This presented some cushioning issues with the seat, and additional movement between the seat and the fuselage.
However, all of the IMUs and other sensors were rigidly attached to each other in the seat-form apparatus, so it provided a good platform for comparison between units.
What the engineers were most interested in was the positioning, velocity and attitude performance under the high G loading, and under the potential partial or full GNSS outages that would occur as the plane’s two GNSS antennas were obscured from the sky with inverted flight at high speeds.
They were also interested in the vibration, temperature and bias performance of the IMUs under these conditions, even though they weren’t extreme environmentally for those parameters. The vibration in particular would not be that extreme in the cockpit; it would be relatively smooth compared to running on a UAV, for example, one of many other applications on which the SPAN units perform.
“We also want to make sure we have the RF recorder there,” Dwyer said. “So, we’re going to be able to reproduce some of our data collection offline, which we can use to simulate different GNSS operating parameters, which we’re pretty excited to do.” Indeed, NovAtel engineers back at headquarters in Calgary, Canada, had extensive plans for post-collection processing and simulation using the data.
“There’s a lot of people’s post processing capabilities that we’re going to get out of this dataset as well, right?” Heidinger assented. “Running with different signals, different signal profiles, different channel configurations, things like that.”
In terms of using external corrections in real time, that was was not the focus of this experiment. But NovAtel engineers plan to do at least some post processing with RTK to compare it with their single-point solution, collecting PPP data as well. That will be post processed as needed with the live data.
Crunching the datasets was an intensive, time-consuming process, with various teams interested in seeing the data for different purposes.
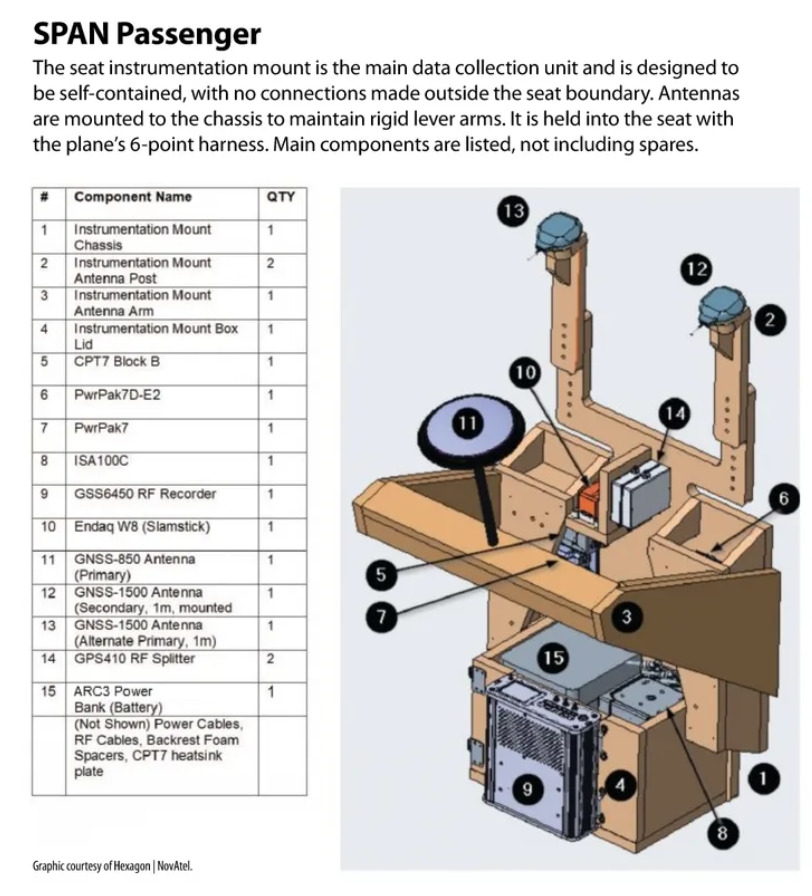
Experimental Challenges
The biggest challenge, Dwyer said, is the fact there’s no feedback to the tester or the user when the system is being run. That requires a solid configuration ahead of time. “And even though it’s relatively compact,” he said, “there’s still a lot of both hardware and software pieces at work here. We’re testing a few different versions of the firmware, depending on what IMU we’re using, things like that. With that many moving pieces, or that many fixed pieces, I guess, there’s a chance something’s going to fail, whether it’s an antenna connector or a power connector or something like that.”
The engineers were all on their toes and everything was checked and rechecked before the L-39 taxied out of the hangar to the runway.
“We’re trying to mitigate all risks,” Heidinger said before the flights, “and I can’t guarantee there’ll be no failures; we’ll view them only as setbacks. We’ll work through those setbacks until we succeed, even flying again, or returning to Florida if we need to.”
Fortunately, and due to the extreme care with which the experiments were designed and conducted, no mishap occurred and there was no need for fallback measures.
Valuable Insights
It can be difficult to know if the entire specific use case for the system is working well with all the different features and sub features, Dwyer said, including dual-antenna GNSS position and heading, and different inertial measurement units mounted in a nonstandard orientation. There’s also managing PPP correction stream and understanding how that is performing in specific dynamics. The team was able to put all these features together during these flights, which isn’t something they get to do in their regular verification and validation testing.
“That’s true from a simple product management point of view as well, Heidinger added. “We’re going to have a flavor of antennas on there. Some are more automotive, let’s say, and other ones are not, they are more true R&D systems. There’s a mix of systems here, a different range of IMUs so we can really characterize our full product line up.”
Not the Last Time
As excited as they were about the imminent airborne reckoning aboard the L-39, active minds at NovAtel were already planning and discussing the next applications to come under scrutiny.
NovAtel engineers always talk about the need for this kind of adventurous testing, this extending the boundaries—into the wide blue yonder, literally—when the discussion turns to simulators and the extensive data runs in that realm. Simulation is absolutely necessary, they readily acknowledge. So is the live testing to go hand-in-hand; one verifies the other, it doesn’t replace the other.
There is an absolute need to verify the models in real-world conditions, and to push them aggressively to discover where their limits may be. To be able to say at the conclusion, yes, we did perform as expected, that’s the ultimate delivery to the customer.
“My hope is that we meet our public performance specs as closely as we can measure them in this situation,” Dwyer concluded. “Obviously, it’s a little tough to measure when you don’t have a real truth system in place here. But with relative comparisons and some offline processing, we’re hoping to hit what our published performance specs are, even though we’re operating far, far outside of the intended range.”
“I’d love to see some of the lower grade IMUs perform beyond expectations,” Heidinger said. “Itwould be great to find out how that cost-effective equipment works and, you know, be like, Wow! This actually did really well on an inverted flight, for example, or a high G and it performed quite well, surprisingly well. We’ll see how that plays out.”
Continue reading (Part Two)…