April 19th saw what some have christened “a second Wright Brothers moment”—namely, the successful first powered controlled flight by an aircraft on another world. Reaching Mars on the underside of the Perseverance rover, the tiny, autonomous Mars Ingenuity Helicopter (5.4’ x 7.7’ x 6.4”) spun its 4-foot rotors and hovered 10 feet off the ground for 30 seconds. By its third flight, a few days later, Ingenuity would rise 16 feet (5 m) up, and fly 164 feet (50 meters) at a top speed of 6.6 ft/sec (2 m/sec).
ABE PECK, Executive Editor, Inside Unmanned Systems
Back in 1903, the Wright Brothers logged 120 feet to complete the first controlled heavier-than-air powered flight. Now, squaring that circle, Ingenuity carries a piece of fabric from the wing of the Wright Flyer, and its flight site is called Wright Brothers Field
Ingenuity represents a culmination of work by, among others, NASA/JPL, a bevy of companies—and AeroVironment. For the major manufacturer of unmanned systems, the flight path to Mars began in 2013, and featured continued collaboration, especially with rotorcraft experts at NASA, and with JPL engineers in the electrical, mechanical, systems and vehicle flight control areas. AeroVironment designed and developed Ingenuity’s airframe and major subsystems, including its rotor, rotor blades, and hub and control mechanism hardware. The Simi Valley, California-based company also developed and built high-efficiency, lightweight propulsion motors, power electronics, landing gear, load-bearing structures and thermal enclosures for NASA/JPL’s avionics, sensors and software systems.
AeroVironment president and CEO Wahid Nawabi summed up his company’s contribution: “AeroVironment’s deep, rich and diverse history of designing reliable and effective unmanned solutions that deliver mission success in extreme environments, combined with our experience with near-space aircraft, make us uniquely suited to collaborate with NASA and JPL. We also incorporated the ultra-lightweight and ultra-high-precision methods integral to Nano projects that have been developed in our MacCready Works Advance Solutions laboratory.”
Subsequent coverage will include other companies’ developmental work. Here, an AeroVironment engineering team will discuss key contributions to Ingenuity’s ability to fly on a planet more than 170 million miles and counting from earth in an atmosphere 1% as thick as ours.
Comments have been edited and reordered for clarity.
BEGINNINGS
Matt Keennon [AV’s technical lead for the rotor system development on the Mars Ingenuity Helicopter Program and an AeroVironment principal electrical engineer. Joined AeroVironment in 1996, and has worked mostly on micro/nano UAVs.]
AeroVironment started as a company making pedal-powered airplanes, unusual man-carrying airplanes, a Solar Challenger. When I came on board in 1996, we were developing small surveillance aircraft for the military, including a flapping-wing aircraft. We did a lot of DARPA work and DARPA does the really far-out difficult things, not knowing necessarily where it’s going to go, what it will be used for. I was really fortunate to head up a lot of little projects that were DARPA-funded, such as the Black Widow [the first micro air vehicle]. We also had the Hornet, which was our first fuel cell-powered small vehicle. And the Hummingbird was the most fantastical flying machine we could ever conceive of—and that was four-and-a-half years of banging our heads against the wall, trying to figure that one out. That was kind of the basis for our weird and unusual flying machines that seemed to suit problem-solving for unusual application, unusual requirements, really difficult customer requests.
JPL asked us how can we demonstrate flight in Mars easily, and when I came on board, I brought in my ideas from those other projects. And that’s why we did the sub-scale. And we also did this other one, which just had a motor and rotor blades. It went up and down on rails, it actually looked like the real helicopter, but it’s just basically an empty fuselage. But they all worked, and served their purpose of getting the excitement and interest levels raised to the next point of funding.
Ben Pipenberg [AV’s engineering lead on the Mars Ingenuity Helicopter Program and AeroVironment senior aeromechanical engineer; joined AV in 2014, worked on sub-scale, larger demonstrators and the final build.]
AeroVironment worked very briefly with JPL in the late 1990s on some proposal efforts for a Mars helicopter; very vague, conceptual stuff that wasn’t funded at the time. But around 2012, 2013, the idea popped back up. The JPL chief engineer for the program came back to AeroVironment and said, “Hey, what do you think about helping out with something like this?” That grew into some small-scale risk tests, essentially just putting a rotor system into a vacuum chamber representing a Martian atmosphere, just demonstrating that we can generate lift.
Early on, there was doubt, even within NASA. With all those early tests, we’re trying to figure out what we don’t know, that we don’t know. There isn’t data out there that tells you how this is going to work or what isn’t going to work right. Coming up with tests that are relatively cheap and easy, and allowed to fail—that’s pretty important.
OPERATIONAL REQUIREMENTS
Ben Pipenberg: Some conceptual designs for what the final helicopter could look like, they were defined as early as 2013. That [involved] a combination of folks, and AeroVironment was doing a lot of the airframe design. But the big challenge with a helicopter like this is that you’re not setting a helicopter on the surface of Mars and then flying it. You’re really designing a small standalone spacecraft that also happens to fly. Before we can ever get to where we spin up the rotors and take off from the surface of Mars, an awful lot that has to occur. And that really defines what a lot of the vehicle requirements are.
The environmental requirements were straight from JPL. And that comes really from the Mars 2020 mission: the Perseverance rover, mission, launch load requirements. The launch vehicle—from an Atlas V, there’s a vibration spectrum we have to survive that defines most of the loads the helicopter is designed against. For controls, there are very specific requirements: natural frequency, rotor blades for hubs, landing gear and all of that flowed down from the JPL-GNC [guidance, navigation, control] team. Sizing constraints was a huge one—what the vehicle is going to have to fit within and unfold from, so there was a lot of work there. And that kind of went both ways, right? AeroVironment saying, “Hey, this is what we need.” And, you know, Lockheed Martin [its Mars Helicopter Delivery System was designed to transport and deploy Ingenuity] and JPL working to accommodate that, and also us working to change the vehicle design to accommodate space available. There was a lot of back and forth on a lot of the environment sets. Environmental requirements were a huge part of it.
Matt Keennon: The wiring inside the mast was kind of like a magic trick. It all had to go in in one piece and then branch out and had to be glued in place.
WEIRD AERIAL ROBOTICS
Ben Pipenberg: The first small-scale demonstrators that attempted controlled flight in the chamber [December 2014] were relatively uncontrollable.
Those initial small-scale helicopters were essentially built the same way we would build a helicopter that flies here on Earth. The problem we ended up having is that, essentially, in a Martian atmosphere you have these rotors spinning really fast, you have very low aerodynamic forces relative to the inertial forces in the rotor. And so the way that the rotor system reacts to control inputs is very different. You also have much lower aerodynamic damping. You can kind of think of it like this really high-speed spinning flywheel you’re trying to control with very low aerodynamic forces, and there’s no damping. So when you see these things flying, they’re kind of all over the place, totally uncontrolled. We didn’t realize that initially, so after we learned that, then, “OK, where do we need to put a lot more time and effort into the analysis? Where is it really going to be paying off for us?”
That was kind of when JPL took on all of the avionics development, all the guidance, navigation control, all the simulation modeling. For the most part, they handled all the batteries, charging solar array, all that. And AeroVironment took on the airframe, a rotor blade design propulsion motors, servo swashplates, the primary structure.
Matt Keennon: Then we went to the full-size demonstrator, the risk reduction, which was really a beautiful piece of engineering, That was the first one that used the full-sized rotor blades. These were all AeroVironment builds; the risk reduction aircraft had the titanium parts that JPL made.
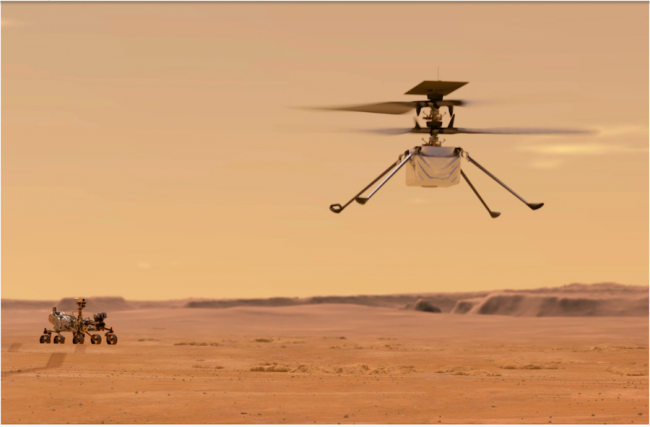
SURVIVABILITY
Ben Pipenberg: In addition to all of those [space and Mars] environments, it has to survive a test environment here on Earth. That that’s where by far the most operating time is spent. Before we ever get to Mars, we’ve already gone through almost the entire operational life of the helicopter. We have to design for all of that. Flying on Mars is relatively benign compared to launching on a rocket in terms of vehicle loads. The hub reaction forces in flight are very small compared to launching on the rocket. That’s really the challenge—you’re not just designing this to fly on Mars, unfortunately; we’re trying to design a very small, lightweight spacecraft that also happens to fly.
ITERATIONS
Matt Keennon: A dozen concepts on paper were never built. The first [built] one wasn’t really a helicopter; it’s a box with a motor and rotors, but that was kind of the first thing that looked like a helicopter. And then for the subscale, there were two versions that had slightly different layouts, different passive stabilization systems.
Then we went to the full-size aircraft. There was one version we called the risk reduction aircraft. And then we get into where Ben is really taking over the engineering design models.
Ben Pipenberg: After that first full-size helicopter, two engineering development models were built. The intention there was that we would start to design what we’d call the flight model, which is Ingenuity, a helicopter on Mars. Two engineering development models were intended to be very similar, that we would be able to test out. One was used for flight testing in the JPL 25-foot-wide space simulator. The other engineering development model was used for environmental testing: thermal vacuum testing, launch loads, putting it on a shaker table and vibrating it, trying to simulate launch, as well as shock testing, radiation and stuff like that. Those two helicopters were functionally similar to the flight vehicle, and what we learned from those helicopters, we would roll into the flight model.
Matt Keennon: We also built something that looked like a helicopter that was just designed for testing the landing gear, the shock absorbers, the angles. We did all this in a motion capture room; it wasn’t a functional helicopter, but it was a functional prototype for testing the landing gear.
Ben Pipenberg: Representative mock-ups to test interfaces and deployments and things like that. Various iterations of other subsystems. Not flyable helicopters, but used to test out flight life representation, different subsystems.
At the end, it all came together. The airframe, the rotor system, the landing gear, all of that was mated to the avionics, the batteries, the solar array, which was a big team effort. Solera developed the solar cells, we developed the structure they’re mounted on, and it was mated onto the rover through Lockheed Martin’s deployment system. A huge team effort. [Our] piece of it is relatively visible—a lot of the pieces you can actually see when you look at a picture of the helicopter, the landing gear that box on the bottom and all the mechanism and structure and rotor blades were designed by AeroVironment.
That final flight model, obviously, that’s kind of the Cadillac version. It had everything built to really survive on Mars.