A comprehensive exploration of the latest advancements in IMU and INS sensor technology.
Manufacturers of tactical-grade Inertial Measurement Units (IMU) and Inertial Navigation Systems (INS) require highly stable and robust inertial sensors to meet the accuracy requirements of dynamic applications operating in constrained environments with high vibration and temperature variations.
“Digital Tactical Grade MEMS Inertial Sensors for Precision Motion Control, Positioning, and Navigation,” a recent webinar hosted by Inside GNSS, Inside Unmanned Systems and Tronics Microsystems, a TDK Group Company, addressed technical solutions for these types of use cases.
A Key Player in Inertial Sensor Technology
Vincent Gaff, Director of Sales & Marketing for Tronics Microsystems, kicked off the webinar. The industry veteran presented an overview of the company’s corporate history and introduced its extensive range of inertial sensors. Operating under the umbrella of TDK Corporation, a global electronics giant, Gaff highlighted the company’s significant contributions to the TDK portfolio. He showcased components like tactical-grade closed-loop accelerometers and gyros known for precision performance.
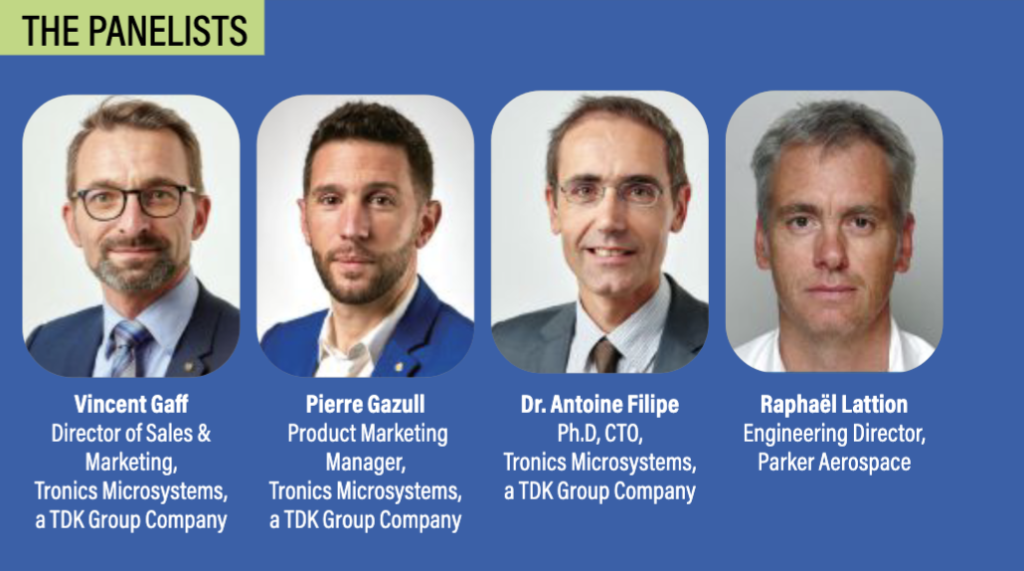
From Design to Performance Metrics
Pierre Gazull, Product Marketing Manager for Tronics Microsystems, shifted the focus to applications requiring tactical-grade inertial sensors. These applications span diverse industries, including electric vehicles (EVs), railway systems, aircraft, marine and subsea applications, and the oil and gas sector. Gazull emphasized the critical challenges of precision and stability in harsh conditions, high dynamics, and extended operational lifetime.
Key considerations for IMU and INS selection were outlined, including low drifting time, stability during outages, and thermal cycling strategies. Gazull also stressed the importance of sensors qualified with vibration and shock profiles representative of the end application.
Gazull discussed the role of sensors in addressing challenges related to high dynamics, low latency and system reliability. Additionally, he underscored the trend in the industry to reduce size, weight and power consumption (SWaP), especially for battery-operated systems like drones and drilling systems in the oil and gas industry.
Tronics Microsystems CTO Dr. Antoine Filipe provided a technical focus on the platform used for inertial sensors and delved into the design details of accelerometers and gyroscopes. He highlighted the closed-loop architecture’s benefits, which achieves significantly better non-linearity compared to open-loop accelerometers.
Performance metrics, including bias instability and angular random walk, were presented for both accelerometers and gyroscopes, showcasing impressive results. Filipe detailed the Application-Specific Integrated Circuit (ASIC) used for MEMS readout and conversion, highlighting its fully hard-coded components and certification processes. The ASIC includes temperature compensation and produces a 24-bit digital output with SPI communication. Filipe concluded with details about temperature compensation, qualification, and the robustness of the sensor architecture, resulting in a high Mean Time Between Failures (MTBF) exceeding 1 million hours.
Decade-Long Collaboration
Raphaël Lattion, Engineering Director for Parker Aerospace, provided an overview of the strong collaboration between the company and Tronics. Parker is an integrator of sensing solutions for aerospace, railway and military applications, with a specialization in harsh environment applications and expertise in safety applications.
The strong alliance is driven by the alignment of Tronics’ MEMS technology with Parker’s technology roadmap. This collaboration has led to two custom MEMS, as well as a MEMS error meter. The collaboration also extends to gyrometers, with Parker Aerospace presenting two performance levels.
Product Portfolio Deep-Dive
In the product portfolio and roadmap segment, Gazull showcased Tronics’ extensive accelerometer lineup. The AXO315 features extended temperature range for precision navigation, tailored for aerospace and oil and gas applications. The AXO305’s navigation, positioning and motion control enables land and marine navigation, and the precision focused AXO301’s acceleration and inclination measurement support railway and industrial applications.
The GYPRO 4300, launched in October 2023, took the spotlight for precise navigation, motion control, and attitude determination. Forthcoming will be the GYPRO 4050, optimized for attitude determination and north-seeking in drilling and survey instruments. Also discussed in the presentation, the Tronics AXO & GYPRO plug and play kit with Arduino platform features a user-friendly GUI based on Tronics’ proprietary software. This enables USB and RS422 outputs and can be directly implemented on testing equipment like rate tables and climatic chambers.
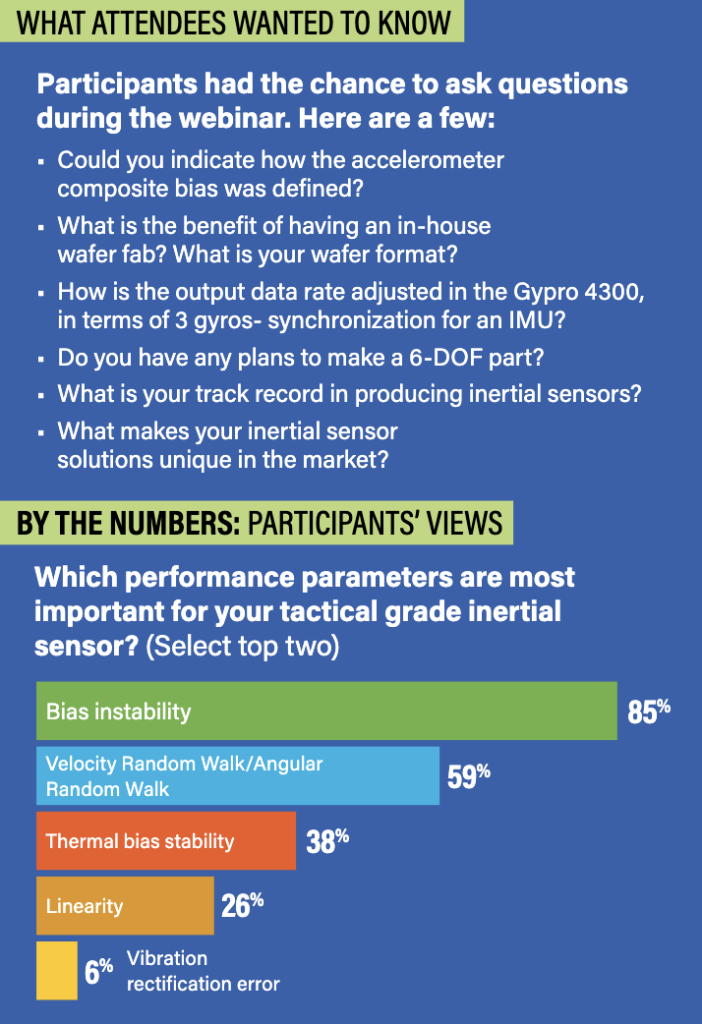
Commitment to Innovation
Looking ahead, Tronics plans to expand its product offerings with application-specific derivatives, addressing varied input ranges, bandwidths and environmental conditions. Gazull emphasized the availability of evaluation boards, providing an efficient means for experts to swiftly assess sensor performance.
To view the presenters’ full remarks, slides and Q&A with attendees, the recording of “Digital Tactical Grade MEMS Inertial Sensors for Precision Motion Control, Positioning, and Navigation” is available for replay online at: attendee.gotowebinar.com/register/3982691035129805152.